I first came across the La Forge Royale miter box when looking through the Benchcrafted blog in preparation for building my workbench. It was an elegant device that was filed away in my mental future project list.
My interest in this appliance resurfaced when researching ways to make small picture frames without holding small hardwood pieces with one hand between the sliding saw fence and the sawblade set at 45 degrees. A miter box was one solution. A Stanley 150 model in good shape and a fair price was bought on eBay and could be used with a Japanese saw ( I stayed away from boxes using Western saws).
After modifying to accept a Japanese saw, it worked but required trimming to achieve a precise 45 degree edge. I sent the box off to my machinist cousin who would work on it between his larger orders. It's been 2 months since I sent it, but given his kind offer to do it for fun, I have not bugged him about it; maybe I'll call him this weekend.
It also seemed when reading about their use that most miter boxes produced results that require additional trimming. A dedicated miter trimmer was an offered solution in these articles but seemed too limited in use to make sense in my shop. In the mean while a Jointmaker SW came up on eBay and for once the bidding on it was not out of control. While with depths less than one inch, it was dead square, when working with thicker pieces there was a slight drift. This got me to thinking about a miter jack again.
They tell me if you can see the line you can cut to the line. That doesn't apply in my case at least when I comes to chiseling across lines interrupted by pins and tails. It became an OCD objective when it became clear that as a dovetail novice, I could use help with that task. Given that deficiency, I would have more use for the 90 degree surface than for the 45 degree face.
An initial obstacle was the wood screw mechanism. At the time I was preparing to start building the jack, Benchcrafted sold the metal parts for connecting the screw to the movable part of the vise.
I was on my own, however, with regards to the wood screw and nut.
I had no interest in learning to make wood screws and nuts or acquiring the hardware needed to make these. Metal screws were used in other DIY variations but these seemed to have either a limited travel range or appear excessively large for the task.
Then I had an Eureka moment where it dawned on me that the solution was quite possibly on my benchtop already- a Veritas quick-release wonder dog.
I began the build 2 weekends ago. DW wanted something to cover a clawed up sofa, but as mentioned above, the miter jack had become an "obscure object of compulsion" to paraphrase the title of an old Spanish movie. I used the Benchcrafted directions for the most part except for a few changes; hence the "populaire" name change.
Instead of 2 inch thick quartersawn maple I glued together 4/4 planks with the rings in alternating direction. Resulted in a little thicker base. I also had the base extend past the fixed jaw for an additional clamping area when held perpendicular.
Instead of a solid block to form the vise jaws with the angle cut with a band saw, I serially ran 8/4 boards through my table saw at a 45 degree blade tilt, then used dominos to maintain position while gluing.
Much to my dismay, the last 45 degree cut exposed the dominos.
The most difficult part of the project was achieving true 45 and 90 degree faces on the jaws. I needed four tries to achieve the final result. Even with use of the table saw for the 45 degree cut, there was a lot of maple end grain hand planing. Painful but necessary as that reference surface is (to keep the French thing going) the raison d'etre for the Jack.
Any possible use for the 22.5 degree insert the Royale featured was not worth the extra effort on my part to make it. If it does turn out to be sufficiently useful, I can add it later on. Thanks to the pattern maker vise and Veritas surface clamps, I can hold the Populaire in a 90 or 45 degree orientation without resorting to making the accessory base
As it turns out, Lake Erie is making a run of the wooden screws and nuts used in the Benchcrafted build. The Royale is prettier and more free-standing than my Populaire, but its $200 saved and I didn't have to wait for the anticipated June delivery. The quick release dog is easy enough to remove and replace if needed
Here is in standard position secured by bench dogs:
At a 45 degree angle:
And perpendicular held by surface clamps:
The next project is something along these lines to cover up and futher protect our poor couch against Andy's claws.
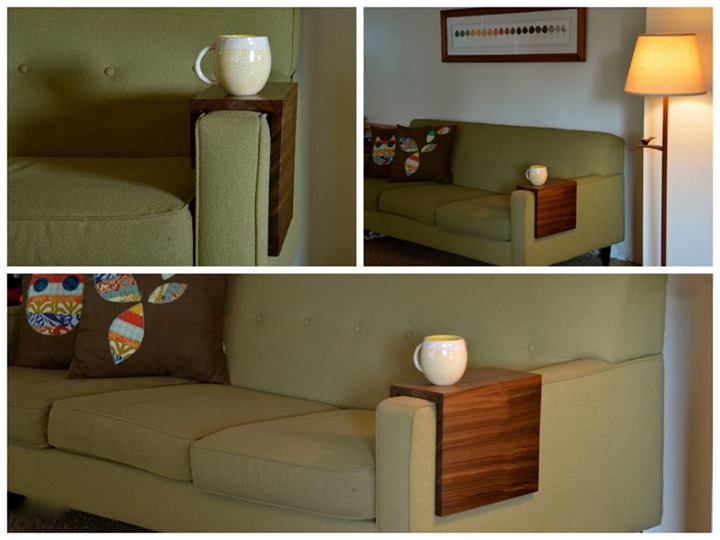
The above is courtesy of She Works Wood- the author is way up on the food chain both as blogger and wood worker.